Warehouse Conveyor Systems
The right warehouse conveyor system can reduce manpower, improve accuracy and increase productivity. We will design you a product feed system completely tailored to your site. Monk’s range of conveyor belt types means we can use standard equipment to reliably handle the size and shapes of your product range. Our goal is to produce a cost effective, reliable warehouse conveyor system with these key benefits:
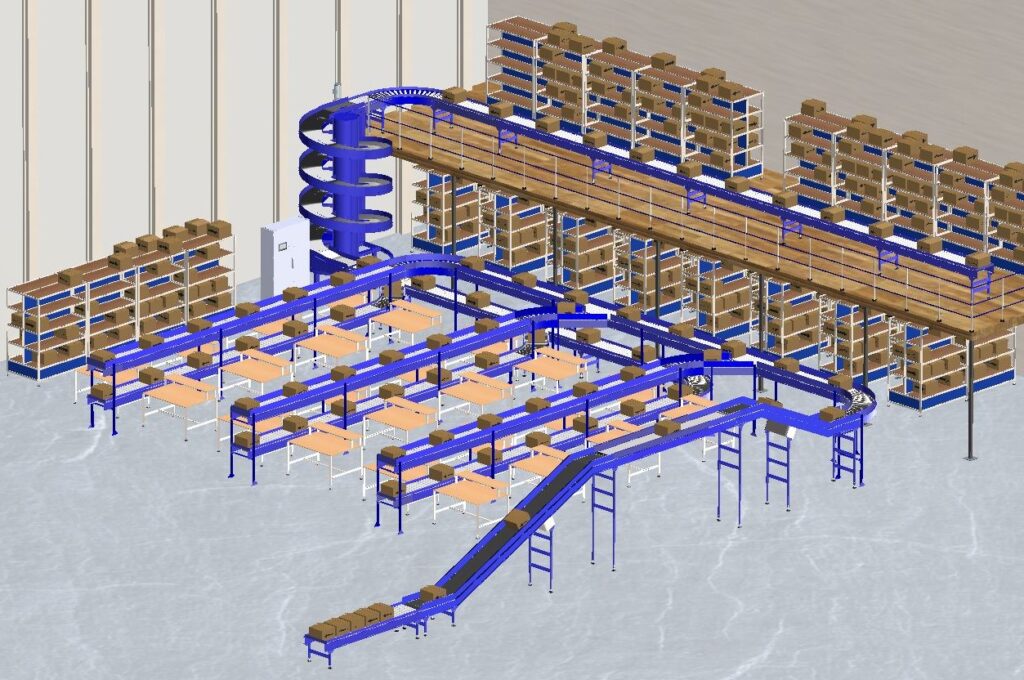
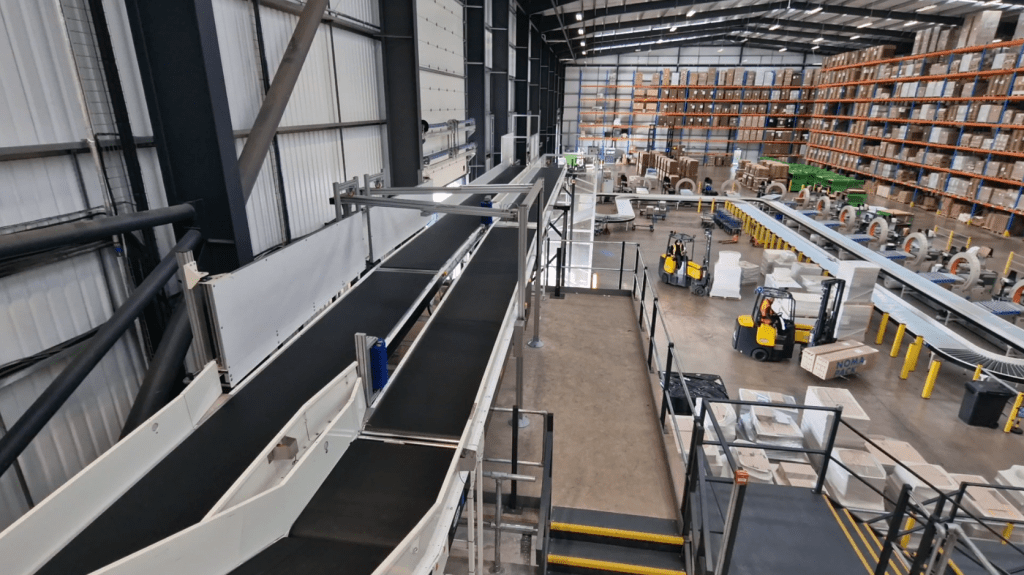
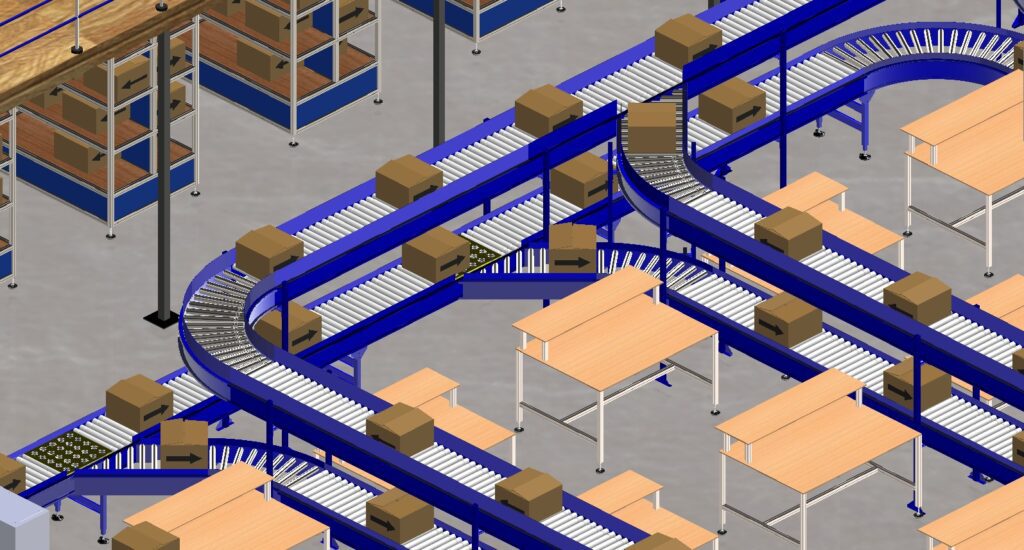
Reducing Manpower – Goods picked from your stores can be placed directly onto a local moving belt and sent to the final packing area, reducing the level of walking or trolley movement and repetitive strain on staff. Operatives will be able to remain productive at their warehouse stations while work is continuously brought to them.
Improving Accuracy – Our Barcode and RFID scanners can route your product to a specific destination. Routing of picked products can be controlled with no product being left behind. Products can be tracked in our system to show locations. Optional Pick to Light faces can be incorporated to improve pick accuracy and speed. Sortation systems can sort product into numerous locations or bins. Our scanning system to Measure, Weigh and Identify Objects at high speeds means we can determine the weight and volume of freight items.
Increasing Productivity – Flow of work is continuous around the warehouse, and even up and down between floors. This is a continuous movement and sets the pace for operatives and machinery to remain busy, reducing idle time.
Being able to provide reliable solutions for warehousing and distribution has become a key part of our business. The first step involves detailed discussions with the customer to understand key areas of your business and its needs.
- The key goals for your site and how our warehouse conveyor system should deliver them.
- Throughput of the entire site and future capacity.
- SKU (stock keeping unit) code quantity and individual SKU throughputs
- Picking location points around the facility and feeding your product or goods to the storage areas.
- Final destination points for products which can be packing benches, dispatch areas, re-packing, courier stillages or robot palletisers.
- Routes available, access, egress, walkways, height and mezzanine floors.
- WMS (Warehouse Management Software) in use and what information is required to route the product to the correct location.
- Barcode or RFID methods.
We’ll arrange a number of meetings around layout drawings to help establish a suitable warehouse conveyor system proposal. CAD models in 3D bring your vision to life and our simulation software can help to prove the workflow and capabilities of our system. A site survey check will show no additional building features or equipment needs to be considered and we can proceed.
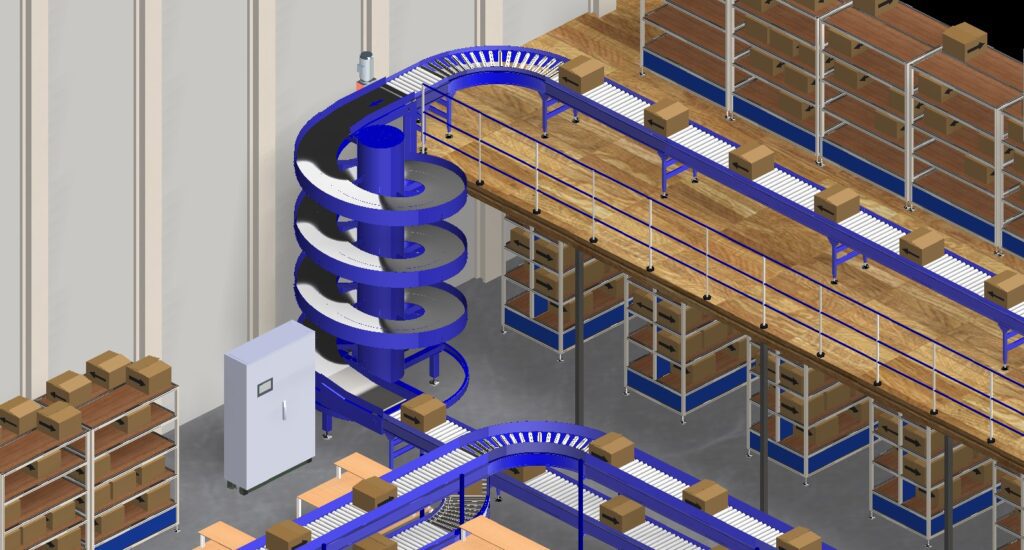
Feeding to and from Mezzanine Floors in the Warehouse
The ability to expand floor space onto mezzanine floors presents the issue of how to get products up and back down. A range of options are available and can be implemented based on products type, throughput, space and budget.
Spirals – Providing a continuous feed of packets, bags, cartons or totes in a low maintenance, compact form. Spiral conveyors have the capability to feed to a number of mezzanine levels with a single conveyor. It’s proven to be the best solution to provide a quiet and smooth operation.
Inter-floor Belt Conveyors – cost effective inclined grip top floor to floor conveyors for sending product to and from mezzanines floors or over walkways to maintain access routes.
Qimarox Lifts – Vertical mechanical lift units for totes, cartons or pallets.
MONK Lifts – Specially designed pneumatic and electric units for specific products.
These are bespoke systems tailored to your product and site. When you call us, we will we discuss the best warehouse conveyor system to get your products between floors.
Solutions for Mezzanine Floor, Racking or Packaging Suppliers
We continue to work successfully with warehouse suppliers which means we can provide conveyor solutions to Mezzanine Floor, Racking or Packaging companies who are putting in new structures for their customer. We will consult with them to provide a warehouse conveyor system with a designed layout to meet the needs of our customer.
We can attend site meetings, provide and share drawings and discuss all the possible layouts. Our experience can help to make the whole process run smoothly and take all the pressure off designing and developing a conveyor system.
Warehouse Conveyor Software and Control
Monk provides bespoke control panels and software to bridge the gap between factory control logic and your existing databases and warehouse management systems (WMS).
We design software that integrates all levels of a SCADA factory control systems, from Programmable Logic Control (PLC) software that controls the moving parts of the system, to application software based on Windows or Linux to control database connections and provide complex HMI’s (operator touch screens).
The most modern and user-friendly touch screens are offered for factory and conveyor control systems, as well as terminal screens to guide operators through a process, and allow for operator input. Our operator control terminals make use of responsive touch screens, and reliable Linux-based computer graphics technologies, which allows for video, photo and document display, complex menu systems and fluid animations.
Every job is unique. Monk will use the most appropriate software technology for the system and warehouse. Software is uniquely written for each job, while re-using common components for maximum reliability. We also use remote access technologies to provide remote dial-in software support, eliminating the need for a site visit for diagnostics and smaller changes.
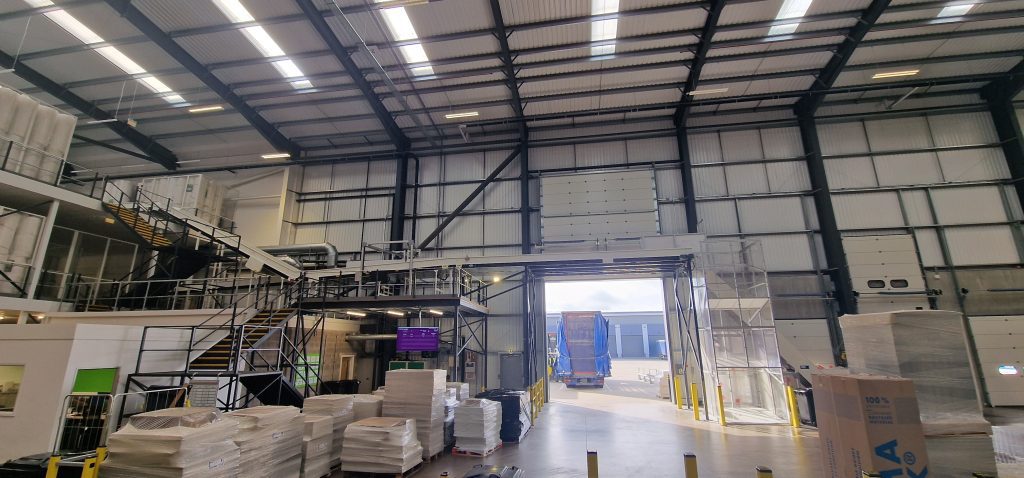
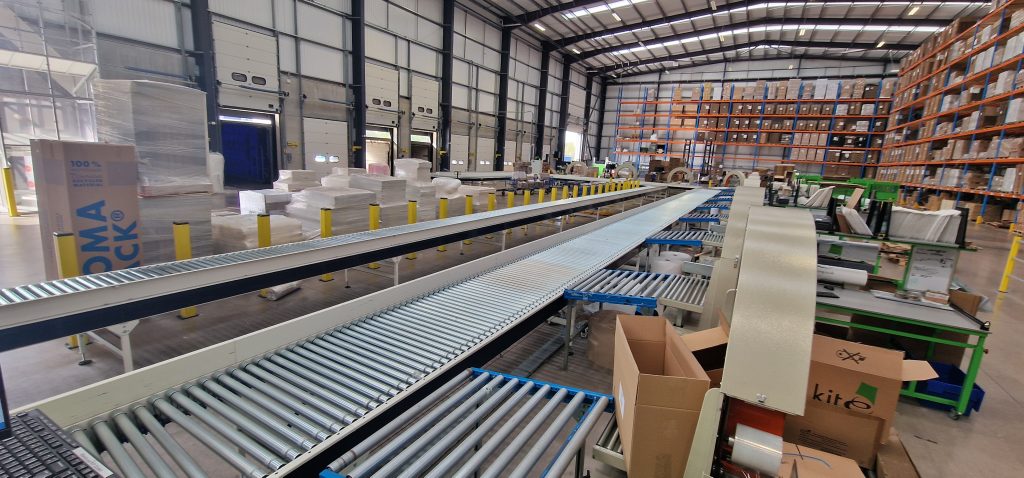
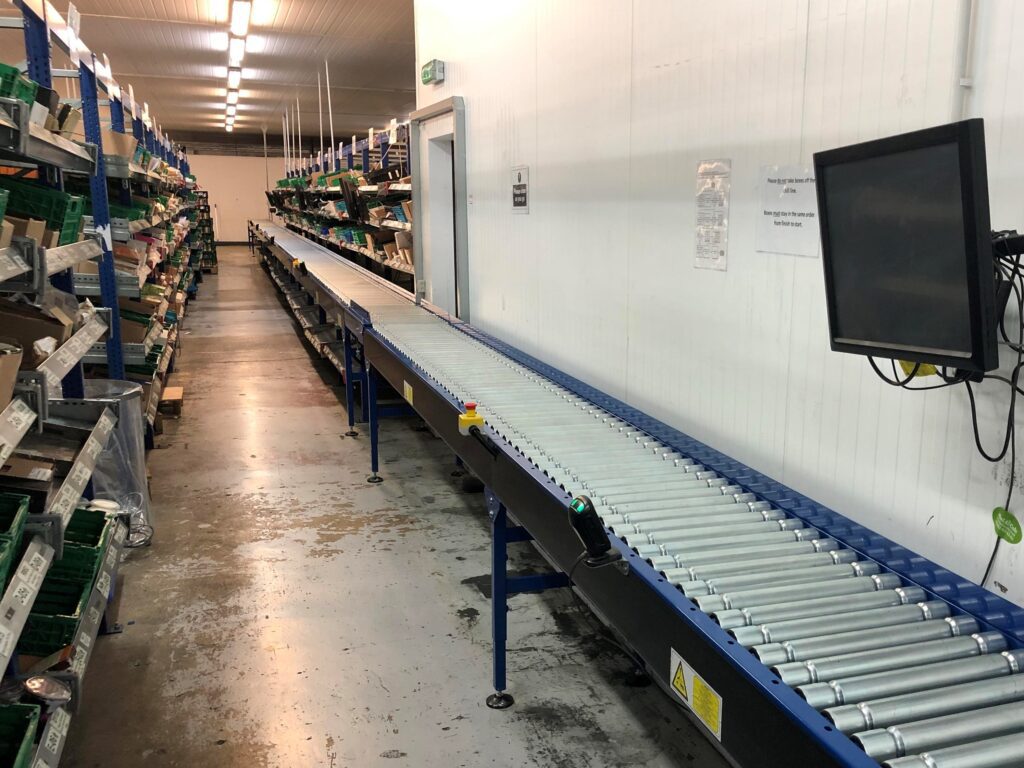
Picking Area
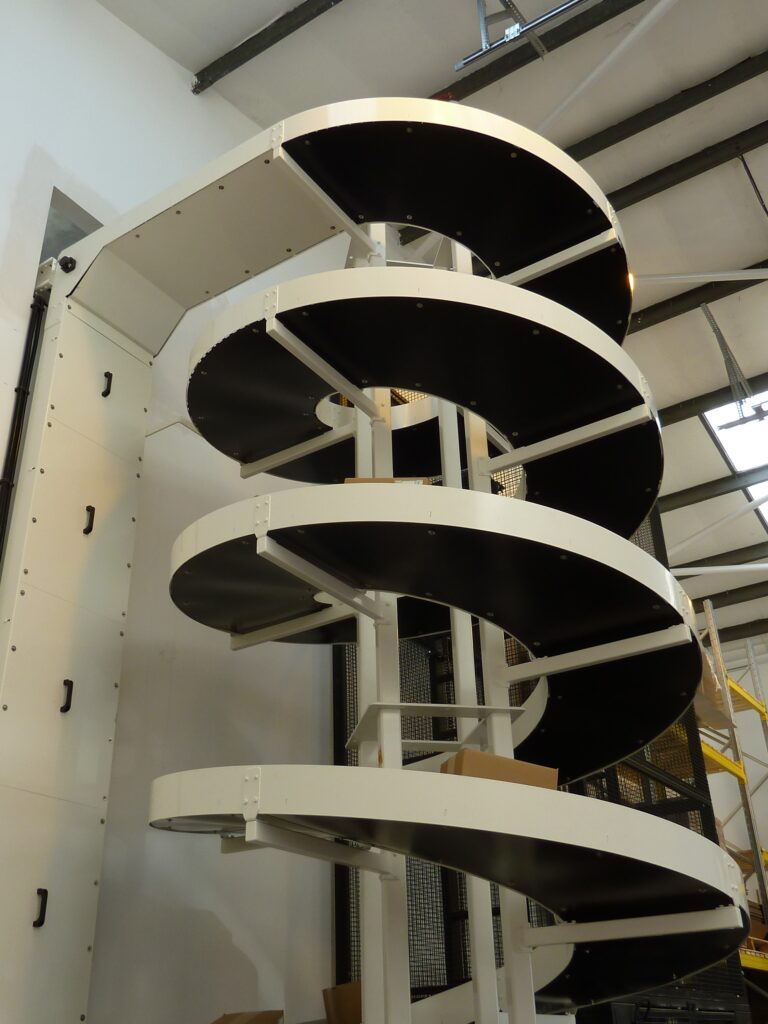
Spiral Down to Ground Floor
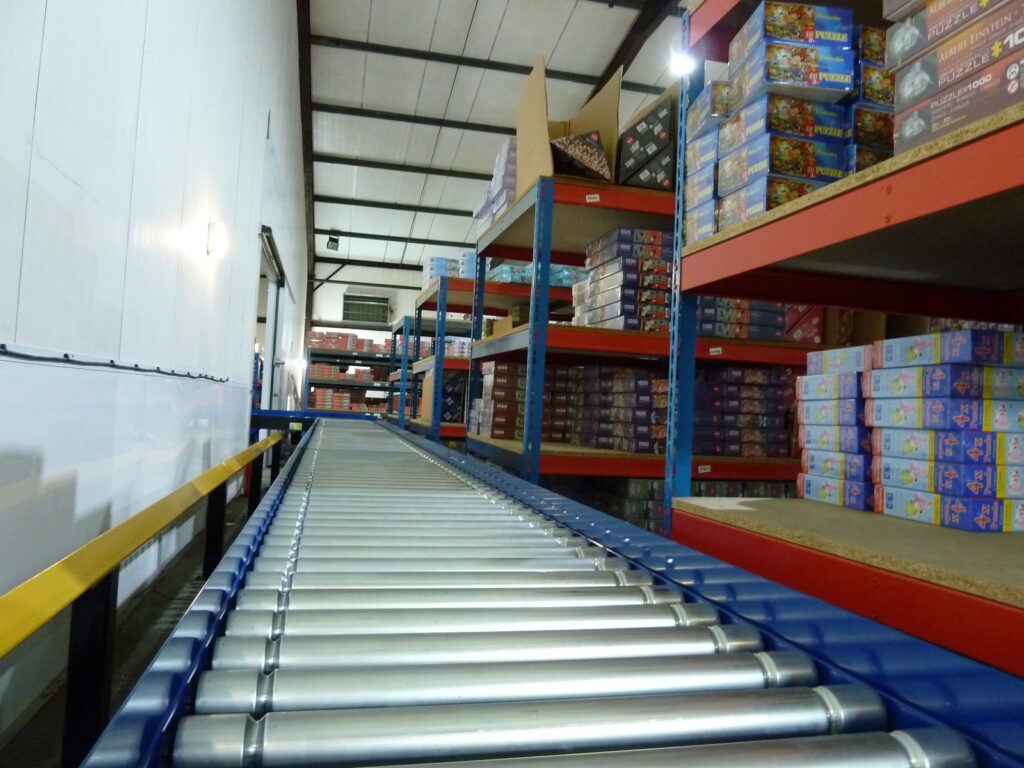
Feed Past Picking Faces
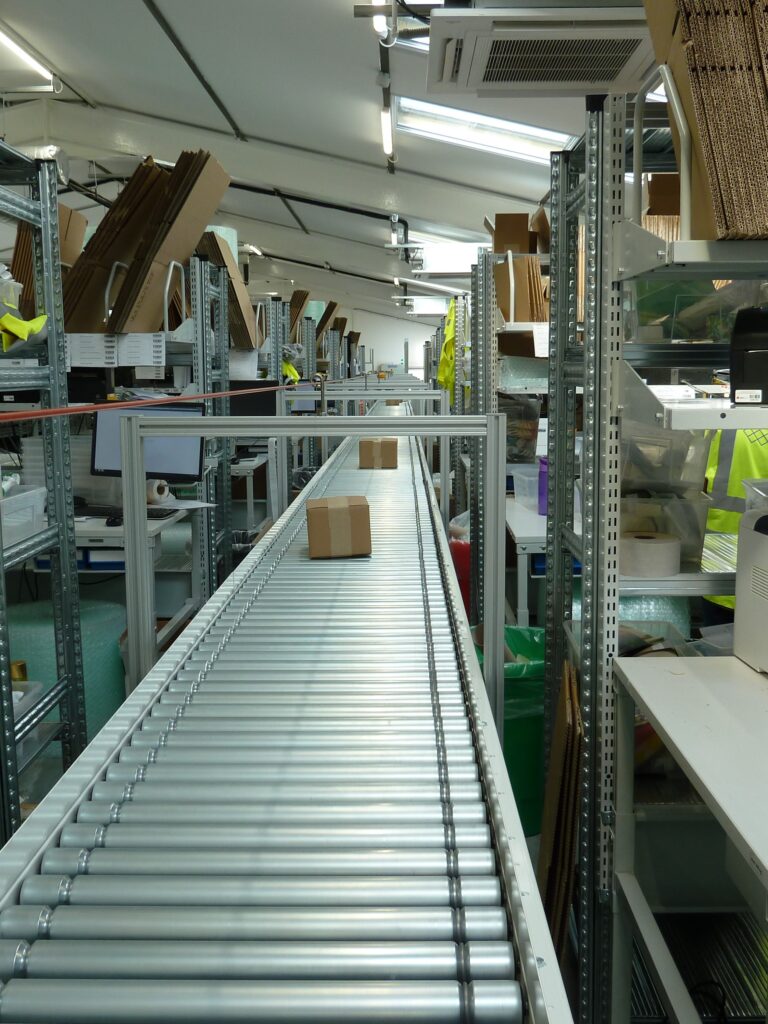