Pick to Light System
A Pick to Light System shows staff quickly and efficiently where they should pick from. The system lights up a tote bin, shelf location or pocket (pigeon hole) within a stores/warehouse area. Staff see the light and know instantly this is the location of the product they need to pick.
“This system maximizes product storage in a small footprint. It greatly reduces picking time and the chance of picking mistakes”
A Pick to Light system can have a massive impact by increasing:
- Speed as staff do not have to look for a location or use memory to know where a type of product is.
- Efficiency because work which is close together can be picked together. Therefore, reducing the amount of walking.
- Accuracy as staff will pick from a location that has a light, there is less chance of an error by picking from the wrong location.
What is Pick to Light? 60 Second Explainer
Pick to Light Introduction and Overview
Pick to Light Process
The typical Pick to Light process uses our hand-held barcode system which would read the barcode or QR code label on both the product and the pick locations. Picking staff would scan a pick sheet, dispatch note or even a carton or tote. Our system would retrieve information relating to that particular Job/Kit. The pick location(s) would light and staff would pick the products. They would scan each product and the location to confirm correct picking. Product can then be handled as a completed job and sent to dispatch or another area of the factory.
Due to each factory or warehouse operating with slightly different methods, our Pick to Light system can be tailored to suit your particular process. The pick locations can be set by a) all of the same Part Number in one location b) all of a Job/Kit in one location.
Location by Part Number: This means that all the parts in one location are exactly the same and staff can pick a single, or number of products from the location when the light is on.
Location by Job/Kit: This means that parts in one location are to make up one particular Job/Kit and therefore may not be all the same. It could be that there are 5 different parts from a number of different suppliers required to make up one complete Job/Kit. As parts are delivered during the day they would be put in the location. When all the parts are complete it would light for picking.
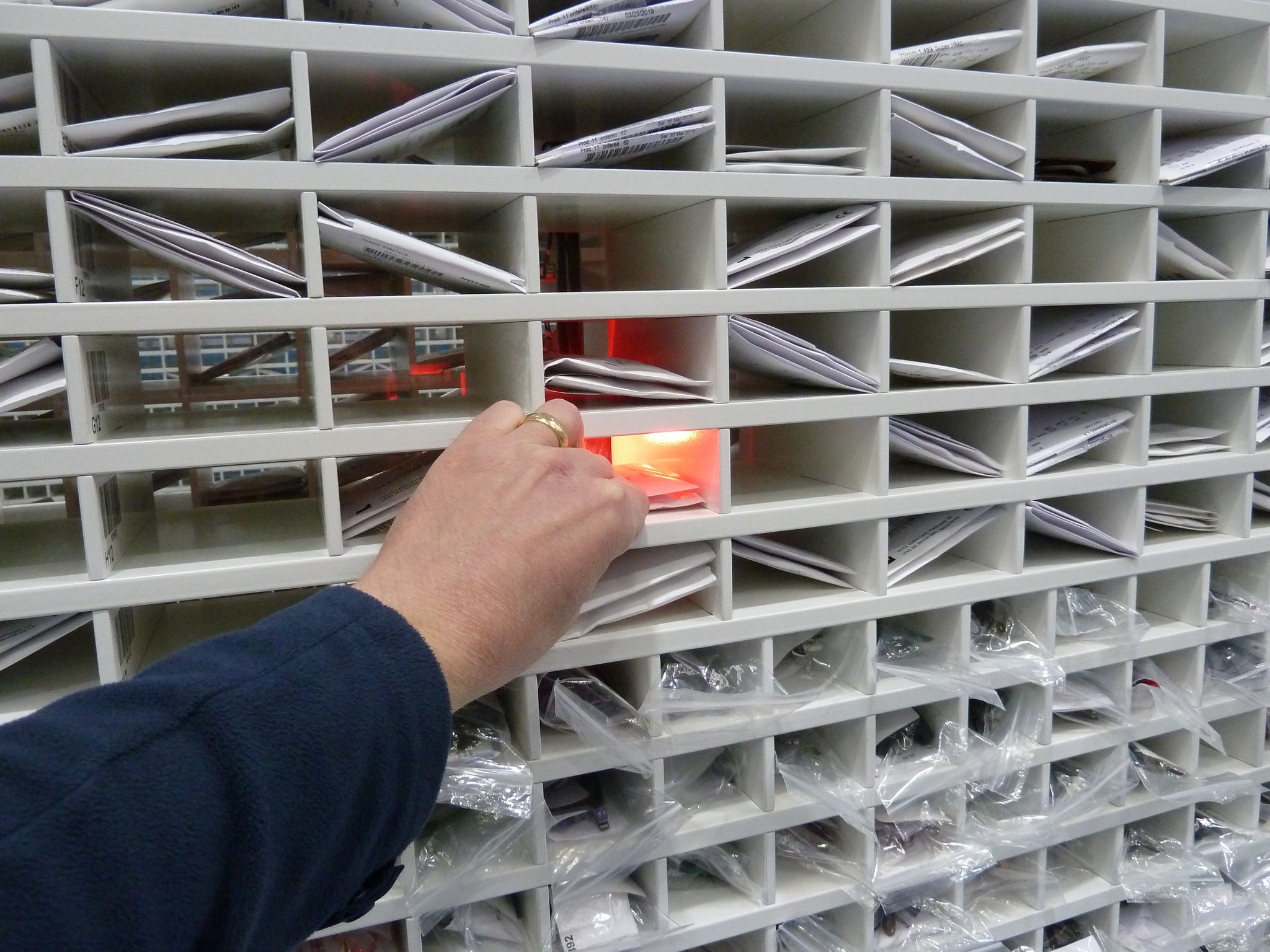
Put Away to Light
The same Pick to Light process can also be used to put products away. A product barcode would be scanned and a location would light up to show staff where to put the product.
Products can therefore be put away by Part Number or to complete a Job/Kit. This can make putting parts away extremely fast and efficient; it will also reduce the chance of products being put in the wrong location.
Due to the size of the storage area, the Pick to Light face is normally split into zones. By grouping together work in zones it reduces the amount of walking and makes it easy for staff to look for the pick light. A typical zone being around 5 to 8 meters long.
Depending on the operation within the factory the same staff can often be used for both picking and put away. A typical scenario is where deliveries arrive in the morning and goods are dispatched in the afternoon/evening. Staff can unpack and put away product as it arrives in the morning and then switch to picking in the afternoon.
Staff can easily switch between Pick and Put Away though the day as deliveries arrive at different times. Due to the efficiency of the Pick to Light system, a small number of staff can operate a large picking area.
Conveyors are often used to bring individual product, trays, tote bins or cartons to the pick face and directly to the correct pick zone. This means that staff can work within a zone where product is automatically brought to them and completed work is automatically taken away once picking is completed. This improves picking and put away efficiency.
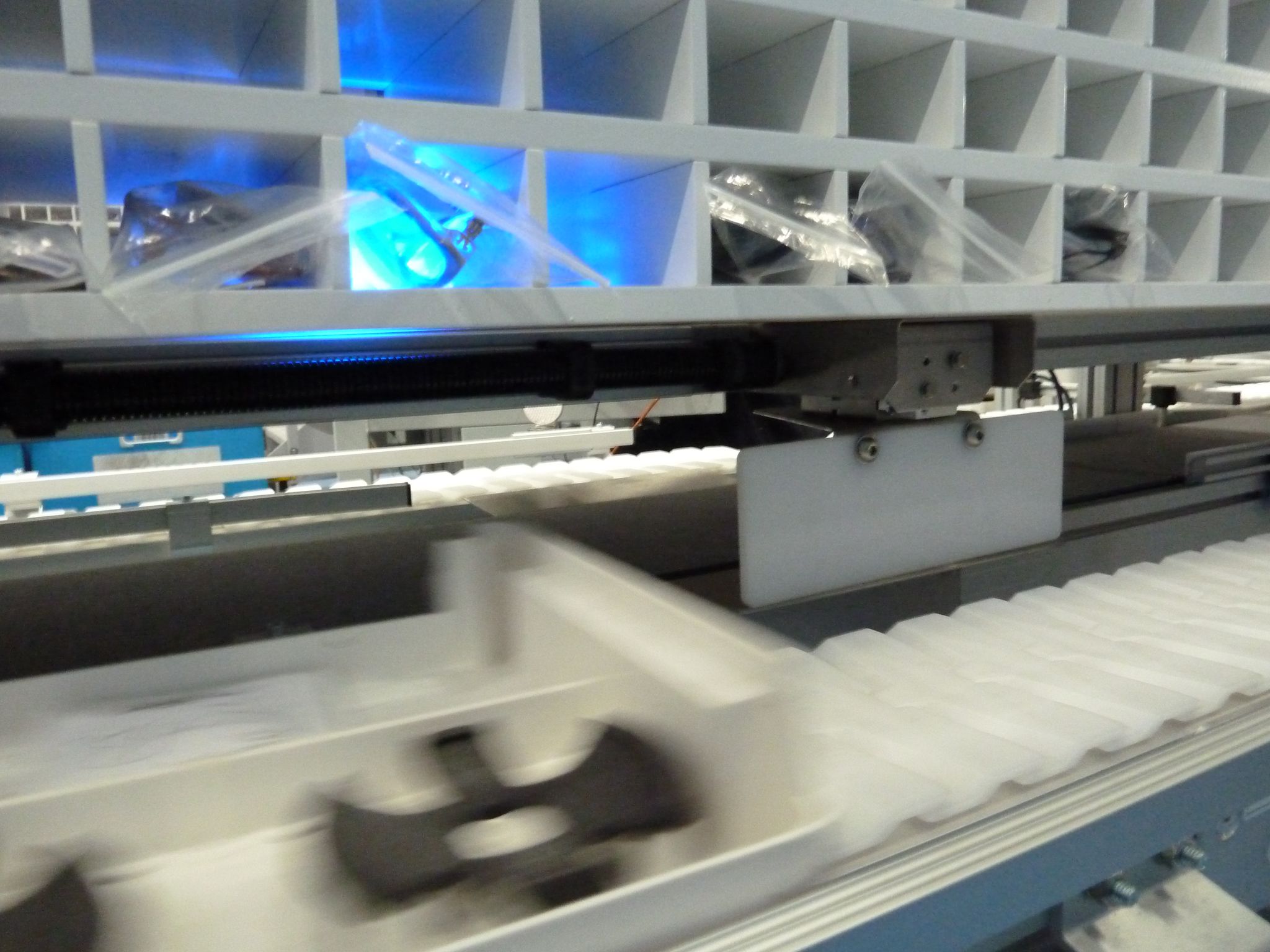
Pick to Light Pockets System Explanation
Pocket – Pick to Light System
Suitable for small products in the Optical Industry, Pharmaceutical, Medical kits, Tablets, Drugs and Dispensary.
This Pick to Light system enables a large amount of product to be stored in a small area with easy and organised picking. Pockets are manufactured to a size that works well with the product and process. Pocket locations can be used to store product by Part Number or Job/Kit.
Pick to Light Bins System Explanation
Bin – Pick to Light System
Suitable for small to medium-sized products in the Optical Industry, Postal, E-Commerce, Pharmaceutical, medical kits, Tablets, Drugs and Dispensary’s. This Pick to Light system enables a larger amount of product to be stored in an area.
Standard tote bins or existing racking can be re-used because our Pick to Light system can be added to the front of existing totes. Systems can be tailored to suit the size and shape of product and the picking process. The system is also easy to expand in modular sections.
Pick to Light Key Features
- Cost-effective design which is customisable
- High and low volume applications
- Compact with minimal floor space
- Built-in modular sections
- Database for part information
- Inventory constantly tracked
- Barcode handheld scanners
- Storage buffer system
- Collates parts together
- Put away and pick parts to light
- Interactive colour changing lighting system
- Minimal staff training required
- Operator Error correction process
- Range of bin and shelving options
Pick to Light Assembly System
The Pick to Light Assembly System allows you to pick and assemble your product in a controlled sequence. It optimises your picking and assembly stations, increasing picking accuracy, speeding up picking operations and simplifying training, resulting in constant, efficient assembly of your products. It reduces the chance of incorrect parts being fitted.
How does a Pick to Light Assembly System work?
The operator will select the assembly type and the quantity to assemble in the batch using the HMI touch screen and MONK software.
Now, the picking process begins. The operator picks the first parts from the green lit bin. The number of parts to pick is shown on the screen and is indicated by the number of white LEDs below the bin.
The system automatically recognises when a pick has been made and the green light deactivates. The operator would then continue to pick the next part and a different bin would illuminate green.
If the Operator picks from an incorrect bin, the entire system will light up in red, clearly informing the operator of the error.
With the parts at hand, assembly can now start. Once this stage of assembly is complete the next green bin is already indicating the next pick location.
Larger parts can be stored away from the pick face in a “Virtual Location”. The location and part number will be shown on the HMI interface screen. The Operator reads the location information, then finds the part, and brings the part back to be used in the assembly.
The Pick to Light Assembly System has many key features which makes it unique and instinctive.
- The HMI allows for intuitive interfacing with the system and can display photo’s, instructions or even video information to the operator.
- On the display, a 3D, real-time mimic of the system is shown, allowing for easy troubleshooting and minimising downtime.
- Each Operator can have a login, which can allow for tracking of performance and tailoring the available assembly lists according to their skill level.
- The menu system allows for Operators to easily find the assembly that they need to pick. This can be tailored to each customer’s needs.
- The size, layout and software can all be adapted in each bespoke build to fit your needs.
- Different product types can be assembled by selecting different bill of materials (BOM’s) on the HMI touch screen.
- To further automate a larger system, conveyors can be integrated with the assembly station to bring in, or take away products.
For a fully customizable, reliable, efficient system for picking and product assembly, Pick to Light, is the way forwards.
Pick to Light and Barcode Software
Our Pick to Light software controls the LED lighting of all locations. The number of locations can range from a few hundred to twenty thousand and above. Our addressable light system eliminates the need for large amounts of wiring leaving a simple and easy to maintain design.
Our ethernet and wireless barcode system means staff can freely move around the warehouse area and pick face using the latest handheld barcode scanners.
Data retrieval is carried out with our Monk Web Call software which will communicate with the customer warehouse management system or factory database software. This enables us to retrieve job information, bills of materials and part numbers to then either store or use for routing and storing product.
Our database system records the location of everything within the Pick Face store.
PC Based with PLC conveyor control
- Automatically starts on PC Reboot
- Password Protected maintenance functions
- 24 Hour Activity Log
- Handshake to PLC
- Informative Alarm system to assist fault finding
- Request Old Data function to upload 24 hours of data in event of a PLC issue.
- Integration of BCR and RFID into the conveyor control system allows HMI display of current job number, relevant job details and job destination
- Colour changing LED’s for clear location info
- Cancelled Order light feature
- Stock Check light feature
Remote access to both the PC/PLC and barcode system means that we can provide comprehensive support and servicing. Please contact us for further information on our Pick to Light Systems.