Warehouse & Sortation Case History

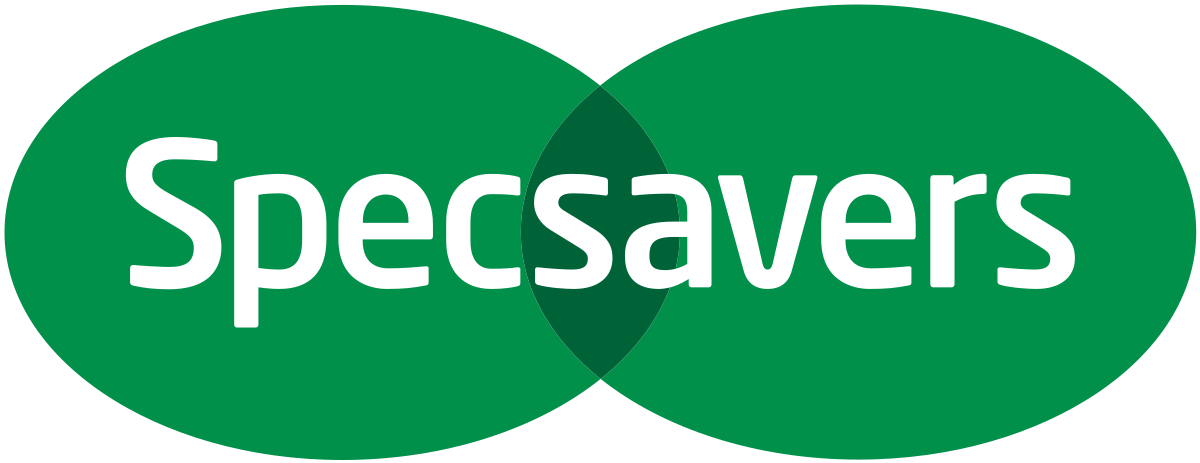
Monk Conveyors latest sortation project transfers flow wrapped packs to 20 postal bins.
Packs are read by our Keyence barcode scanner; we then communicate with the WMS to retrieve job information. This is compared to a reference list and a bin location is known. Pack position is tracked with an encoder fitted to the conveyor drive.
Product is blown from the track into one of the 20 bins, optional mechanical diverter arms are available for larger products.
An illuminated push button tells operators when a bin is ready to be changed and a simple press of the button stops further product being blown to the bin while this is taking place. Product was supplied at 1400 per hour with higher speeds available.

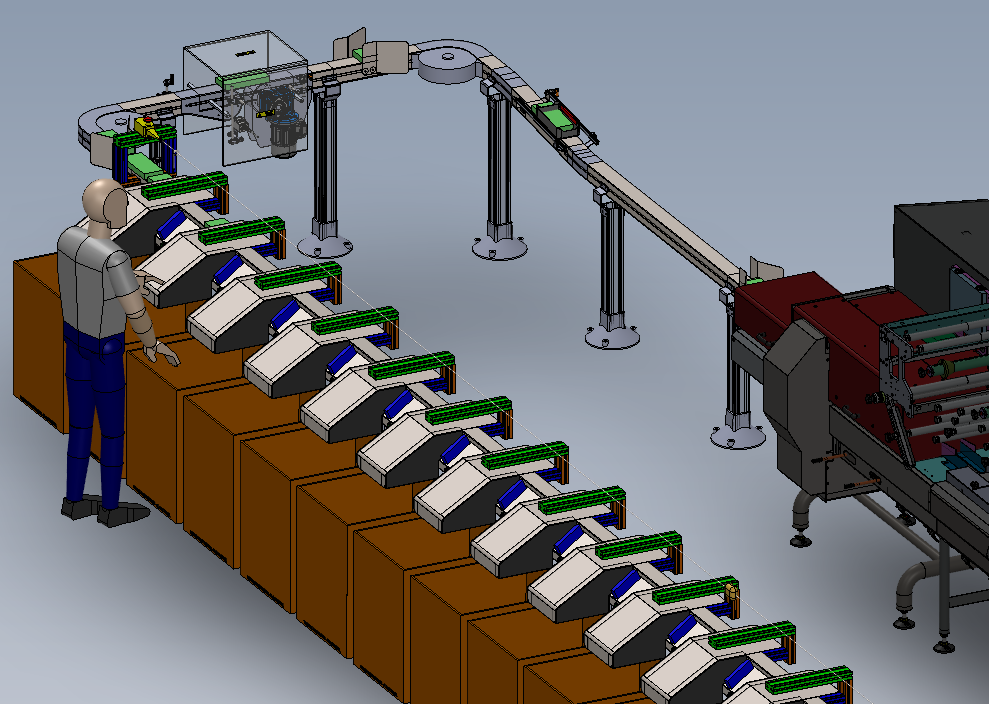
Space restrictions were overcome using MODU 83mm wide friction chain to take product from the flow-wrapping machine round 90-degree bends to the sorting area.
The design concept was proposed to the customer in 3D CAD so they could clearly visualise the system and discuss the idea with staff and operators.
This led to a number of design improvements which could be put in place before the system was delivered and installed.