Cleanroom Conveyor

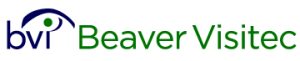
Medical and Pharmaceutical Case History
Beaver Visitec is a leader in products for ophthalmic surgical procedures. We have carried out a number of projects to help automate their manufacturing facility in Warwickshire, most notably the design and installation of a new cleanroom conveyor. Our previous experience designing conveyors for a cleanroom helped us appreciate the environment the system would be operating in.
The cleanroom conveyor system uses one of our standard two door airlocks to allow work to be fed on conveyor into the cleanroom, while minimising loss of clean air. Within the cleanroom we designed a conveyor feed system which would transfer trays 240 x 255 x 45mm in front of an automated picking system.
Operatives would then pick from racks all the components required to complete a surgical kit, before allowing the tray to be automatically sent onto the next part of the process.


The trays then line up in the packing area using a ‘zero line pressure’ controlled system. This means that an operative can remove any job tray from the line and work on it. When they remove a tray the cleanroom conveyor automatically moves all the work forwards. This means operators are constantly fed work which is easy to remove from the line. Empty trays are placed on a lower conveyor so they can be returned to the start.
All surfaces were designed for easy cleaning. The system saved an operative continually moving product out of the cleanroom on trolleys. It also maintained a continual flow of work through the picking area and other processes in the cleanroom.
The project included full mechanical and electrical installations, followed by training and handover to the customer.
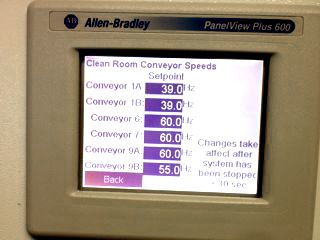
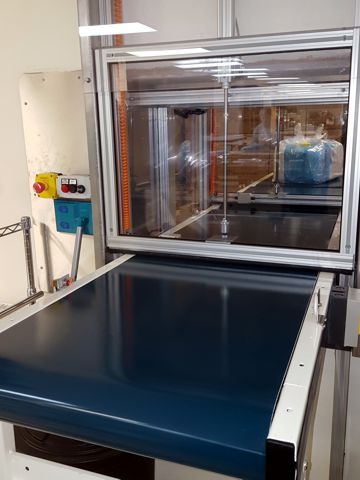